The purpose of blowing is to remove particles, rust, semi-stick material and heterogeneous material (welding residues, sand, etc.), present in steam systems. These substances, formed during the rolling phases or during plant construction, can cause serious damage to equipment powered by this piping (steam turbines and turbines) and cause serious problems during the preliminary phases of plant running.
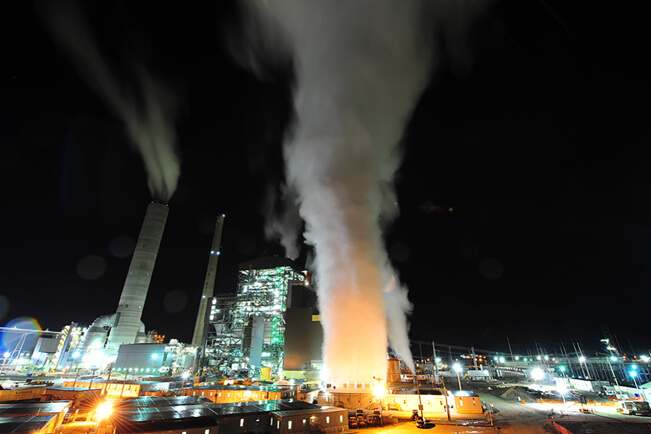
The measurement of the degree of cleaning is carried out through the so-called DFR. The DFR “Drag Force Ratio” is the factor that measures the amount of movement in the blowing conditions compared to the operation conditions.
In fact, if you are in the “stricter” blowing conditions than the operative ones (DFR > 1.2), you get progressively removing all vehicle particles.
Therefore, blowing is preparatory activities for the commissioning of steam systems, steam turbines, steam generators, refineries steam networks, etc. These activities are strictly necessary, as systems that are not fully cleaned prior to operation could affect the integrity of the turbines and the operation of the valves and instruments, harming themselves.
WCS specializes in this type of activity by providing three different blowing methods depending on system geometry, utility availability, available times and economic factors. All three methodologies are equally effective.
The peculiarities of each type of blowing are described below.
Continuous low pressure steam blowing
The characteristics of this method are:
- Great efficiency
- Drastic reduction in runtime
- Low noise
This method allows you to blow continuously, for a long time, at a speed close to the sonic, keeping the noise level at low values (<75 db at 30 meters from the muffler) and maintaining a fairly low pressure (<7-8 bar).
Calculations are performed to check the appropriate steam speed to ensure cleaning.
The ability to operate uninterrupted reduces cleaning time, costs and a guaranteed result.
Steam blowing is a critical activity when commissioning thermal power plants and steam systems in general and, for this reason, it is important to reduce as long as possible to perform this operation.
By adopting the “Silent Steam Blow” the results are obtained in a short time using superheated steam at low pressure.
Advantage of the low pressure steam blow (quite steam blowing)
- Continuous blowing
- Low noise <80 db
- Reducing blow times
- Achieve low-pressure cleaning
- Steam flow requirement ca. 30% -50% of maximum capacity
- No need for special supports
- No Stress analysis for permanent piping is required
- High Economic Benefits
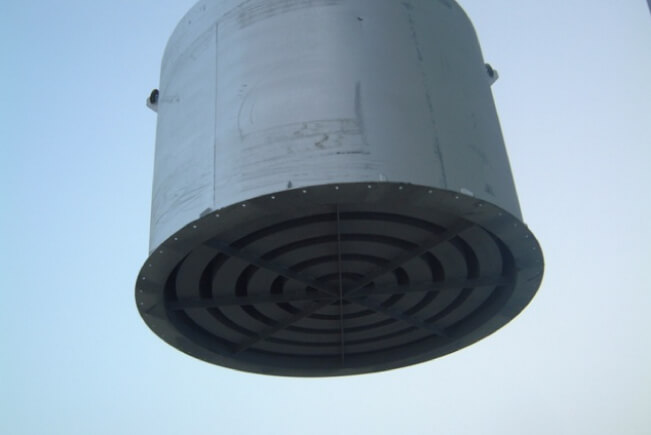
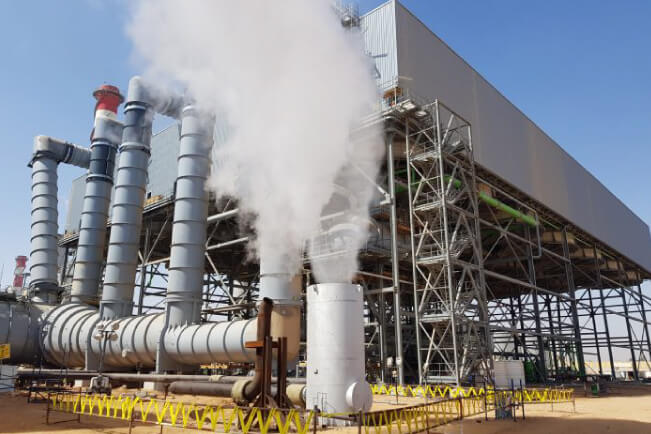
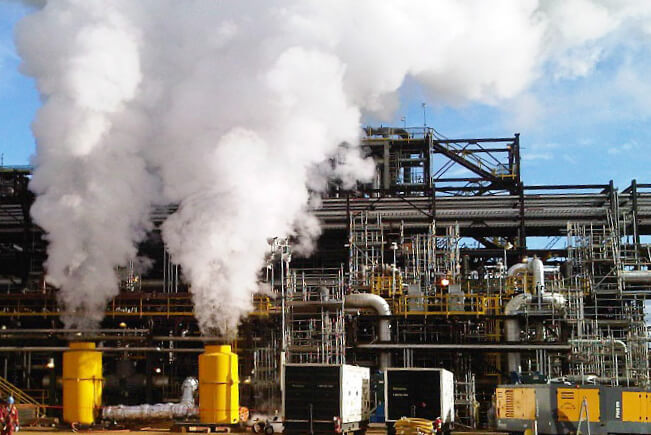
Discontinuous Blowing
These blows are performed using a traditional method, often used, in the past, in thermoelectric plants. Once the expected pressure has been reached, according to the engineering, the blow valve (provisional) is opened and, quickly, the steam contained in the system is released through the pipe line and the muffler. For a short period of time, the steam reaches the correct DFR (the factor that measures blowing conditions) by cleaning the system lines. This method uses medium and high pressure steam, produces high thermal and mechanical shocks in systems and, for this reason, requires precise engineering calculations and stress analysis for piping system, consequently with high rating material. Adopting this methodology, the value of the DFR is reached for a few seconds/minutes for each valve opening and hence the time required to achieve the required cleaning quality is longer than the “Silent Steam Blow” method described above.
The disadvantages of this method are:
- Discontinued method
- High noise > 120 dB
- High number of blow cycles
- Longest blowing time: 2-4 weeks for the clean system
- Steam lines subject to high mechanical forces and thermal stress
- Special support for blowing lines with necessary stress analysis studies
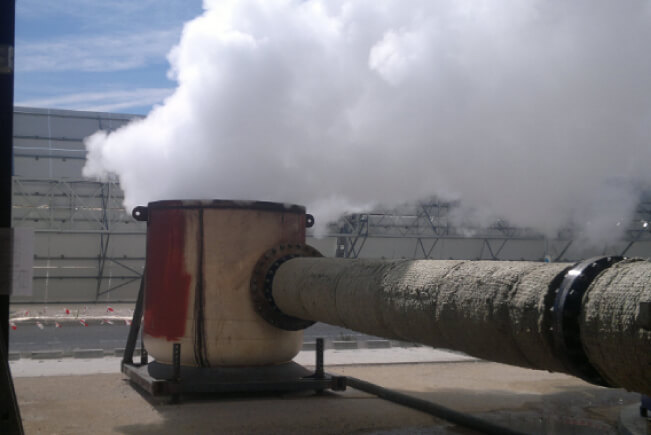
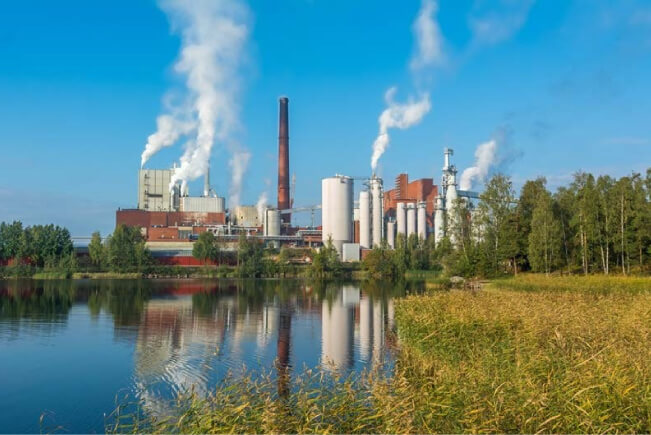
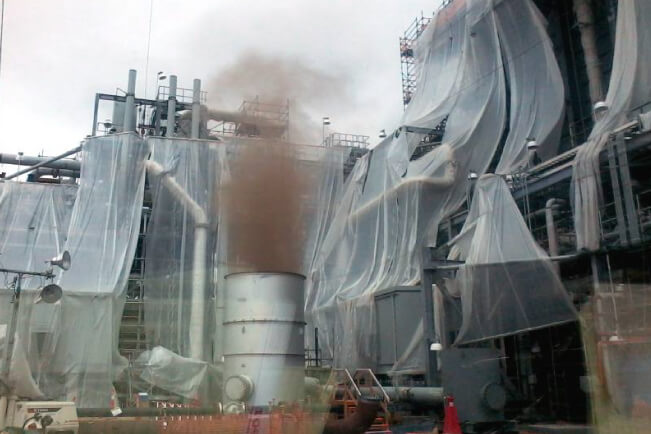
Air Blowing
The advantage of air blowing comes from the fact that it can be done without having the gas turbine available. The operation can be performed even before you have the turbogas commissioned and ready for production. This makes the blowing independent of the start-up of the turbogas and being able to advance start-up activities, increasing production days.
The method is based on the implementation of cold-type discontinuous blowing cycles, in which, after a pressurization phase, the air accumulated in the systems is released quickly thanks to the opening of quick-opening sacrificial valves. The operation, to be effective, must be designed and carried out under conditions that guarantee a greater amount of motorcycle than that obtained in operation, placing the witnesses on the trajectory, to check the degree of cleanliness.
The features of this method are:
- Discontinuous method
- High-pressure blowing cycles
- Instantly create high flow rates
- Using a quick-open valve (sacrifice valve)
- High-strength forces with effective debris fluidization
- Significant reduction in cleaning programming time and subsequent commissioning
- It can be carried out before the start-up of the plant